In the modern electronic and electrical industry, engineering plastics have been widely used because of their excellent properties and versatility. Engineering plastics have high strength, heat resistance, corrosion resistance and insulation properties, and are ideal materials for manufacturing various electronic and electrical products. Engineering plastics with higher performance and stronger environmental protection are constantly used in the communication field of electronics and electrical appliances, laying the foundation for the manufacture of high-performance, multi-functional and portable electronic equipment and communication products.
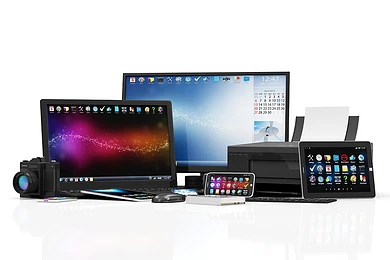
Advantages of Engineering Plastics in Electronic Appliances
High Strength and Durability
Engineering plastics exhibit excellent mechanical properties, including high strength and rigidity. They can withstand high loads and impacts, with good fatigue strength and durability. Typical engineering plastics like polycarbonate (PC), polyamide (nylon) maintain their properties even under harsh conditions.Extends product lifespan, reducing maintenance and replacement costs.
Superior Electrical Insulation
Engineering plastics generally have excellent electrical insulation properties, effectively preventing current leakage and electric shock risks. This makes them ideal for manufacturing electronic and electrical products.Improves the safety and reliability of electronic products.Widely used in electrical components, connectors, sockets, and insulating parts.
Heat Resistance and Flame Retardancy
Many engineering plastics, exhibit extremely high heat resistance, maintaining stable performance in high-temperature environments. Additionally, these materials possess flame retardancy, providing extra safety in emergency situations like fires.Suitable for applications in high-temperature environments,Enhances product safety, meeting stricter fire safety standards.
Chemical Resistance
Engineering plastics can resist corrosion from a wide range of chemicals, including acids, alkalis, solvents, and oils. This chemical resistance makes engineering plastics widely used in fields such as chemical processing, medical devices, and food processing.Suitable for manufacturing equipment and parts that require long-term exposure to chemicals.Extends the service life of equipment.
Lightweight and Design Flexibility
Engineering plastics have a lower density compared to metals, significantly reducing the weight of products. Additionally, engineering plastics are easy to process and mold, enabling complex and intricate designs to meet various innovative needs.Enhances the portability and usability of products, such as handheld electronic devices and portable tools.Improves production efficiency and reduces manufacturing costs.
Environmental Friendliness and Sustainability
Many engineering plastics are recyclable, meeting modern industrial requirements for sustainable development. Effective recycling can reduce environmental burden.Complies with environmental regulations and standards, enhancing corporate social responsibility image.Reduces waste and resource wastage, promoting the development of a circular economy.
Application Cases
Engineering plastics play a pivotal role in enhancing performance, reliability, and longevity across various applications in the electronics and electrical industry. Their unique combination of mechanical strength, thermal stability, electrical insulation, and chemical resistance makes them indispensable for manufacturing advanced electronic devices, components, and systems. As technological advancements continue, engineering plastics will continue to evolve, meeting the increasingly stringent demands of modern electronic and electrical applications.